If you are doing multiple pours of epoxy to achieve your desired thickness, or perhaps the result of your first pour didn’t come out exactly how you expected, then you may be wondering if you can epoxy over epoxy. When using epoxy, it can be a helpful process to add a second layer, but you want to make sure to follow the correct procedures.
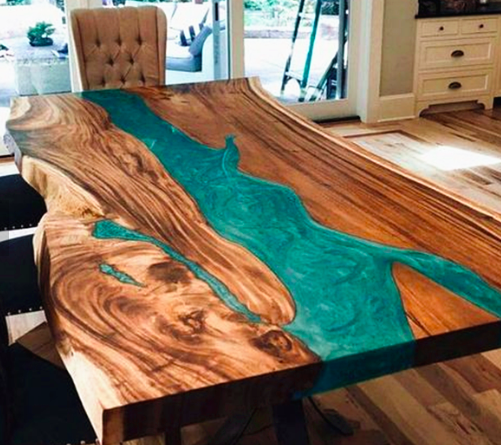
With most coating epoxies, if you are trying to build up to your desired thickness, it is recommended to pour your second coat once the first coat is tacky to the touch (usually 4-6 hours). However, if the coat is hard and has cured, its best to sand the surface before you re-pour in order for the second coat of epoxy to adhere to the first.
If your surface is hard to the touch, follow these steps to prepare for your second coat, and what to do to make sure that your final finish comes out nice and smooth.
Can You Sand Epoxy?
Now, you might be asking: can you sand epoxy? The answer is, yes. In fact, it is an important factor in being able to add a second layer of epoxy. You can also give your surface a light sanding in order to achieve less gloss/shine if you desire. But thats a tutorial for another time...
First, if you're epoxy has cured properly and is hard to the touch without imperfections, you can do a light sanding with 320-grit sandpaper in order to scuff the surface so that you can apply your next layer. If your epoxy has not cured properly or you have imperfections, its important to take care of these before you pour your next layer. If your epoxy is still tacky after 12 hours, it is likely didn’t mix the correct ratio of resin and hardener, or you did not mix them thoroughly. In this case, you would need to remove the tacky areas and sand it down, otherwise the layer will remain tacky underneath the new layer or epoxy and you risk your top layer not curing properly as well. This video goes into more detail on how to do that...
Preparing for the Second Coat
When you are all done with the sanding and are happy with the smoothness and evenness of the surface, then you need to begin preparing for the application of the second coat. To do this, you want to make sure that you have a clean surface and work environment that will be free of debris and dust. These things may end up in the epoxy as it dries and sticks to it. This will cause imperfections and may leave the item in the layer.
Cleaning the area that you will be working in will go a long way to keep your epoxy resin clear of dirt and dust or other particles that could show up in it once it is dried. We suggest using Isopropyl Alcohol 99%. It is important that you use 99% as anything else will have water in the alcohol, and epoxy and water do NOT mix.
After you have cleaned the area liberally, then you will want to ensure that you have a new container to mix your resin in. The container that you used last time, for the first coat, will not work because any unmixed epoxy can contaminate your next batch.
Get a fresh container and stirrer, and measure out the 1:1 ratio precisely, or as directed by the brand you are using. If this is not done well, then your resin will not harden as it needs to and will end up with a sticky finish that feels wet to the touch. Once this happens, there isn't a way to fix it without adding more resin, which costs more, so you want to double-check this stage every time you mix to ensure that you are doing it properly and not wasting any mixed product, especially because you won’t be able to use it again.
-Top Epoxy Pick-
Pouring the 2nd Coat
When you have sanded down the first coat and finished preparing for the second coat, then you are now ready to pour on the second layer of epoxy resin. When doing this, you want to be generous with your pour so that the entire area is well coated with liquid and the self-leveling feature will work better. It is also best to mix a large amount at a time so that you can pour continuously before the resin hardens, and so you do not run out mid-pour.
Pro Tip: Always have more epoxy on hand than you think you might need. If you run out of epoxy in the middle of your surface, you cannot simply add more to the surface later as you will likely see a visible line where the first and second pour meet.
You also want to use a heat source to pop any air bubbles that may form while the epoxy resin is leveling out. As you pour the mixture onto the first layer, there may be some pockets of air that form bubbles, and using the heat source to pop them and smooth out the area will stop the resin from starting to harden, which can keep the bubble in place and enable you to see the air bubble in the finished coat.
Then, you will let the second layer cure for 12-24 hours. You can continue this process to build the coat to your desired thickness.
Conclusion
Adding a second layer of epoxy resin can be a great way to fix leveling issues, get rid of imperfections, build up the thickness and ensure that your surface has hardened properly so that you have a solid surface once the resin has fully cured. Following these tips will ensure that you get the best results so that your project comes out as good as possible.